Future of Work: Running the Robots
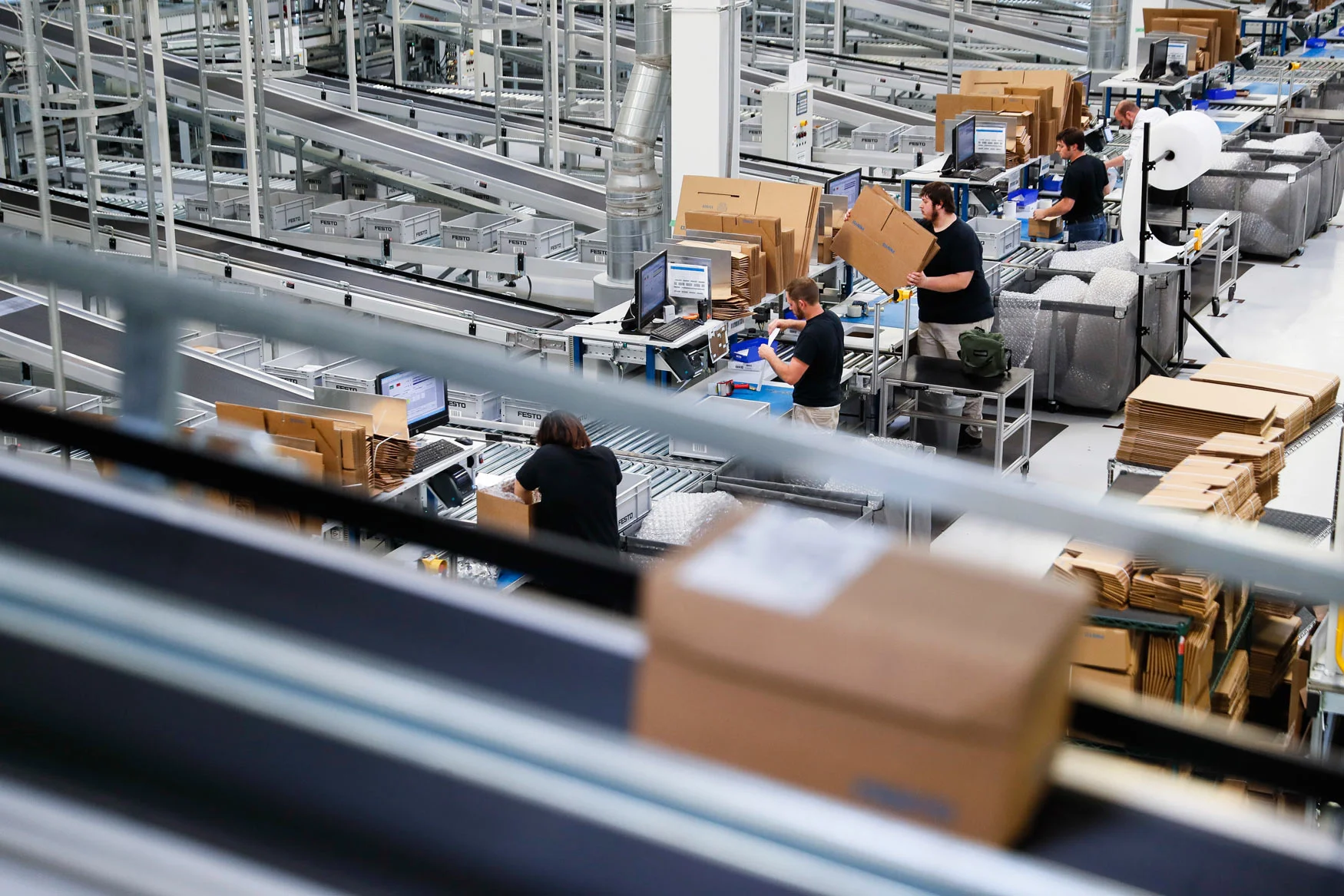
This is part of the first installment of Future of Work, an Associated Press series that will explore how workplaces across the U.S. and the world are being transformed by technology and global pressures. As more employers move, shrink or revamp their work sites, many employees are struggling to adapt. At the same time, workers with in-demand skills or knowledge are benefiting. Advanced training, education or know-how is becoming a required ticket to the 21st-century workplace.
__
Herbie Mays is 3M proud, and it shows — in the 3M shirt he wears; in the 3M ring he earned after three decades at the company's plant in suburban Cincinnati; in the way he shows off a card from a 3M supervisor, praising Mays as "a GREAT employee."
But it's all nostalgia.
Mays' last day at 3M was in March. Bent on cutting costs and refocusing its portfolio, the company decided to close the plant that made bandages, knee braces and other health care supplies and move work to its plant in Mexico.
At 62, Mays is unemployed and wants to work, though on the face of it he has plenty of opportunities: Barely 10 miles from Mays' ranch-style brick home in this blue-collar city, GE Aviation has been expanding — and hiring.
In this Friday, April 14, 2017 photo, Herbie Mays pauses during an interview at the Ohio Means Jobs employment assistance offices in Cincinnati. Mays voted for Donald Trump, drawn to his pledges to stop American jobs from going overseas and to revitalize manufacturing in the United States. Trump's election, though, "was too late to help us," Mays said. "If you don't keep up with the times, you're out of luck," he said. (AP Photo/John Minchillo)
In the state-of-the-art laboratory in a World War II-era building the size of 27 football fields, workers use breakthrough technology to build jet engines that run on less fuel at higher temperatures. Bright flashes flare out as GE workers run tests with a robotic arm that can withstand 2,000 degrees (1,090 Celsius).
The open jobs there are among 30,000 manufacturing positions available across Ohio. But Mays, like many of Ohio's unemployed, lacks the in-demand skills.
"If you don't keep up with the times," he said, "you're out of luck."
This is the paradox of American manufacturing jobs in 2017. Donald Trump won the presidency in great measure because he pledged to stop American jobs and manufacturing from going overseas, winning Rust Belt votes from Mays and other blue-collar voters.
In this Wednesday, May 17, 2017 photo, a robotic conveyor uses laser guides to sort through materials storage at Festo's distribution facility in Mason, Ohio. "This kind of factory has nothing to do with the factory we knew in the 1960s or 1980 or even 2000," said Yannick Schilly, vice president for North American business for Germany-based Festo, a global industrial automation company. Floors clean and aisles uncluttered, the plant is mostly quiet as workers monitor a robotic distribution system that self-adjusts its work flow to prevent backups. (AP Photo/John Minchillo)
It's true that many jobs have gone overseas, to lower-wage workers.
But at the same time, American manufacturers have actually added nearly a million jobs in the past seven years. Labor statistics show nearly 390,000 such jobs open.
The problem? Many of these are not the same jobs that for decades sustained the working class. More and more factory jobs now demand education, technical know-how or specialized skills. And many of the workers set adrift from low-tech factories lack such qualifications.
Factories will need to fill 2 million jobs over the next decade, according to a forecast by Deloitte Consulting and the American Manufacturing Institute. Workers are needed to run, operate and troubleshoot computer-directed machinery, including robots, and to maintain complex websites
In this Thursday, May 25, 2017 photo, an assembly line laborer works across from a collaborative robot, right, at the Stihl Inc. manufacturing facility in Virginia Beach, Va. At the plant human workers are interspersed with computers and robotics that require trained technicians to service and maintain while reducing the company's need for pursuing traditional manual laborers. (AP Photo/John Minchillo)
Last year, software developer was the second-most-common job advertised by manufacturing companies, behind only sales, according to data provided by Burning Glass Technologies, a company that analyzes labor market data.
Yet the United States for now remains a follower, not a leader, of the trend. Workers in many European and Asian countries are more likely to be working with robots than U.S. workers, studies show. In such countries as Japan and Denmark, robotics and advanced automation have created solid jobs while increasing efficiencies for manufacturers.
Trump continues to make promises about adding U.S. manufacturing jobs. In blue-collar Youngstown, Ohio, he talked about passing by big factories whose jobs "have left Ohio" on his way to a July 25 rally, then told people not to sell their homes because the jobs are "coming back. They're all coming back."
In this Thursday, May 25, 2017 photo, a robotic forklift autonomously transports materials throughout a Stihl Inc. production plant in Virginia Beach, Va. The self-driving forklifts deploy flashing lights and constant beeping sounds to navigate around corners, through doors, and operate safely around their potentially unpredictable human counterparts. (AP Photo/John Minchillo)
But Sen. Rob Portman, an Ohio Republican and a former U.S. trade representative, conceded in an interview: "We're not going to see the kind of manufacturing renaissance that we all want in this country unless we focus on skills training."
Labor Secretary Alexander Acosta, in a visit to a Detroit factory in June, acknowledged the need to address the skills gap by developing advanced computing skills. And when Trump visited Pewaukee, Wisconsin, in June, he touted the value of training while doing.
"Apprenticeships teach striving Americans the skills they need to operate incredible machines," Trump said. "This is not the old days. This is new and computerized and complicated."
Of the 146 million jobs in the United States, only about 0.35 percent were filled by active apprentices in 2016. Filling millions of open jobs through apprenticeships would require a substantial increase in government resources. So far, the Trump administration has called for more funding but hasn't made any progress securing the funding from Congress.
In this Wednesday, May 17, 2017 photo, workers operate packaging stations that feed into an expansive system of conveyor belts connecting separate factory areas at a Festo distribution center in Mason, Ohio. "None of these technologies work without the people," said Carolin McCaffrey, head of Learning Center Midwest for Festo Didactics, which last year launched two-year apprenticeship programs in mechatronics. Skip Johnson, a trainer in STIHL's apprenticeship program, said the key is getting bright students into plants, where they see that the grimy, dusty factories they have seen in books and movies are giving way to clean operations using futuristic technology. (AP Photo/John Minchillo)
Apprenticeships are much more common at some European companies, notably German firms. At Germany-based Stihl Inc.'s plant in Virginia Beach, Virginia, for example, A.J. Scherman is learning to be a "mechatronics technician." Mechatronics combines electrical and mechanical engineering as well as computer skills.
Stihl makes chain saws, leaf blowers and weed trimmers at the factory. Once he's completed his final year in Stihl's four-year apprenticeship program, Scherman will read diagnostic software on computer screens attached to each robot to repair and upgrade them. If necessary, he'll hook up a laptop to program changes.
Scherman, 37, is also earning a college degree as part of the apprenticeship. Thanks to financial aid from Stihl, he'll finish with zero debt.
In this Thursday, May 25, 2017 photo, A.J. Scherman, 37, left, works with fellow apprentice Ryan Buzzy, 18, right, on a robotics control computer at a chainsaw assembly line at a Stihl Inc. production plant in Virginia Beach, Va. Scherman, with only a high-school degree, wanted to earn more money when his daughter was born and took a chance with a mid-life career change. Scherman is earning a college degree as part of a Stihl apprenticeship and will finish debt-free thanks to financial aid provided by the company. "We're safe, because we're the guys who fix the robots when they malfunction," Sherman said. "We're going to need people to fix the more advanced systems. This program trains us." (AP Photo/John Minchillo)
Skip Johnson, Stihl's apprenticeship coordinator, said it's critically important to bring bright students into the plant, where they can see that the grime and dust they associate with factories are giving way to clean operations using futuristic technology.
"They just come in here, and they're wide-eyed," Johnson said.
U.S. manufacturing workers, excluding managers, make an average of $44,000 a year, according to government data. That's just 2.8 percent higher, adjusted for inflation, than a decade ago after years of shifting of jobs overseas or to nonunion states. And it compares with a much higher 8 percent gain for the labor force as a whole over the past decade.
But a typical mechatronics engineer with a four-year degree can earn $97,000 a year; a typical software developer makes just over $100,000.
Festo Didactic, the education arm of Germany-based Festo, last year launched two-year mechatronics apprenticeship programs in Ohio with Sinclair Community College, and is already expanding its U.S. apprenticeship offerings. At Festo's plant in Mason, workers monitor a robotic distribution system that self-adjusts its work flow to prevent backups.
"This kind of factory has nothing to do with the factory we knew in the 1960s or 1980 or even 2000," said Yannick Schilly, who heads global supply for Festo's North American business.
But there's not much demand locally these days for the kind of repetitive tasks done in those factories by workers such as Herbie Mays.
He acknowledged that there are "plenty of jobs out here.
"What you have to do is get training or education."
In this May 25, 2017 photo, employees work a factory floor at a Stihl Inc. production plant in Virginia Beach, Va. There are assembly lines at the Stihl plant, but human workers are interspersed with computers and robotics. Two robot arms in one corner of the plant tie cords to the black pull handles used to start the company's outdoor power tools, a mundane job formerly done by people. With the efficiency gains comes a calmer, more open and orderly workspace that contrasts with the traditional stereotype of chaotic, dirty manufacturing plants. (AP Photo/John Minchillo)
In this May 18, 2017 photo, engineering instructor David Campbell, center, assists his students as they operate a robot designed and built for competition by their fellow classmates at Colerain High School in Cincinnati. Campbell's team entered into the 2017 FIRST Robotics international high school robotics competition, serving as a showcase for local talent while encouraging students to pursue engineering, software development, and technology design fields. (AP Photo/John Minchillo)
In this March 7, 2017 photo, Colerain High School students in Cincinnati huddle in groups to design and build a robot for the FIRST Robotics competition. The international contest draws corporate sponsors looking to recruit students interested in engineering, software development, and technology design careers. (AP Photo/John Minchillo)
Apprentices stand at workstations at the automation learning center at the Festo distribution facility, Wednesday, May 17, 2017 in Mason, Ohio. Lou Morales, who trains the apprentices, understands the negative images associated with manufacturing. Years ago, he showed up at his steel mill at Glen Cove, New York, to find he no longer had a job after it shut down suddenly. "I've never seen so many padlocks in my life," recalled Morales, 60. But now he assures young people that "the future is endless" for them in manufacturing because new kinds of jobs are being created and the skills they are learning are in high demand. (AP Photo/John Minchillo)
In this May 25, 2017 photo, apprentice Ryan Buzzy, 18, right, works with Skip Johnson, left, a trainer for the Stihl Inc. apprenticeship program, on a metalworking lathe in their training area at the Stihl Inc. manufacturing facility in Virginia Beach, Va. Buzzy is being trained as a "mechatronics technician" at Stihl, which makes chain saws, leaf blowers and weed trimmers at its factory in Virginia. Mechatronics combines electrical and mechanical engineering, as well as computer skills. After completing Stihl's four-year apprenticeship program, he will read diagnostic software on computer screens attached to robots for repair and maintenance. (AP Photo/John Minchillo)
In this Wednesday, May 17, 2017 photo, an employee stands at her workstation at the Festo distribution center in Mason, Ohio. As manufacturing automations grow, specialized technical jobs are forecasted to increase. The need to fill those jobs "will happen very quickly," said Yannick Schilly, vice president for North American business for Germany-based Festo, a global industrial automation company. "Those who are positioning themselves the best to cope with technical evolution will be the winners of tomorrow." (AP Photo/John Minchillo)
In this Thursday, May 25, 2017 photo, an assembly line laborer works alongside a collaborative robot, left, on a chainsaw production line at the Stihl Inc. production plant in Virginia Beach, Va. Despite efficiency increases and lessening the need for manual laborers, companies require workers who can program, oversee, operate, and maintain the automation. A report by Deloitte Consulting and the American Manufacturing Institute estimates 2 million such jobs will need to be filled over the next decade. (AP Photo/John Minchillo)
In this Thursday, May 18, 2017 photo, a robotic arm with a high-intensity blowtorch is remotely operated to test ceramic matrix composites, which make engines more durable, heat-resistant and efficient, at the General Electric Aviation plant in Evendale, Ohio. At GE Aviation, internships and co-ops with colleges attract younger prospective employees, while veteran workers are retrained. The giant Building 700 is home to white-coated scientists clustered in the FastWorks Lab nestled inside the decades old building, while much of the rest is relatively quiet. (AP Photo/John Minchillo)
In this Thursday, May 25, 2017 photo, a giant robotic arm loads pallets full of chainsaws prepared for shipping at the Stihl Inc. production plant in Virginia Beach, Va. Despite efficiency increases and lessening the need for manual laborers, companies require workers who can program, oversee, operate, and maintain the automation. A report by Deloitte Consulting and the American Manufacturing Institute estimates 2 million such jobs will need to be filled over the next decade. (AP Photo/John Minchillo)
In this Thursday, May 25, 2017 photo, an assembly line laborer works alongside a collaborative robot, left, on a chainsaw production line at the Stihl Inc. production plant in Virginia Beach, Va. Despite efficiency increases and lessening the need for manual laborers, companies require workers who can program, oversee, operate, and maintain the automation. A report by Deloitte Consulting and the American Manufacturing Institute estimates 2 million such jobs will need to be filled over the next decade. (AP Photo/John Minchillo)
In this May 25, 2017 photo, an employee works on a factory floor at a Stihl Inc. production plant in Virginia Beach, Va. There are assembly lines at the Stihl plant, but human workers are interspersed with computers and robotics. (AP Photo/John Minchillo)
Text from the AP news story, As the laid-off struggle, high-tech US plants offer jobs, by Dan Sewell and Christopher S. Rugaber.
Rugaber reported from Virginia Beach and Washington, D.C. Contributing to this report were Associated Press business writer Yuri Kageyama in Tokyo, AP writer Jan M. Olsen in Kalundborg, Denmark; AP videojournalist Mike Householder in Detroit, and AP photographer John Minchillo in Cincinnati.
Photos by John Minchillo
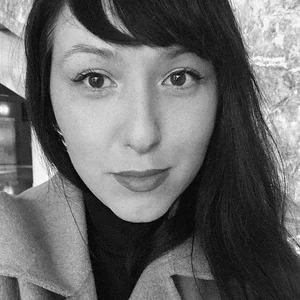
Visual artist and Journalist